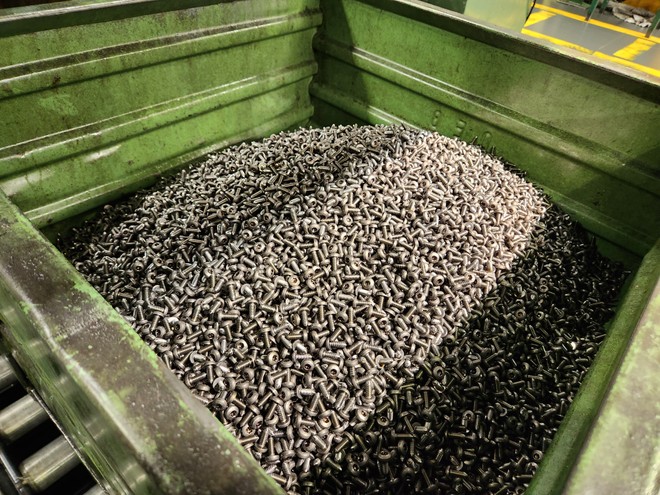
Brugola è un nome noto, specie per un brianzolo come me che qui ci è nato e cresciuto, mai contagiato dal fascino della grande Milano. Infatti OEB è una di quelle aziende che, pur avendo quasi 100 anni alle spalle non molla l’Italia, anzi. Resta fedele a quella piccola porzione della Brianza dove tutto ebbe inizio, dividendosi fra Lissone e Desio.
UNA STORIA ITALIANA A CONDUZIONE FAMILIARE
Nata nel 1926 da Egidio Brugola, l’azienda ottiene nel 1945 il brevetto della vite cava esagonale con gamba a torciglione, migliorando nettamente la vite a testa esagonale che era stata inventata negli Stati Uniti da W.G. Allen.
Brugola, diventato subito eponimo utilizzato anche da chi non ha la minima idea di chi sia stato Egidio e di dove abbia sede l’azienda italiana che è un vanto nel mondo, riuscì a risolvere la criticità del progetto di Allen andando a migliorarne la tenuta utilizzando il gambo a torciglione. Nasce la “vite a brugola”.
Sono proprio le caratteristiche di resistenza meccanica, unite ad un controllo qualità altissimo che controlla ogni singolo pezzo (e ne scarta molti), che hanno fatto dei prodotti di Brugola qualcosa di fondamentale nel mercato automotive.
Quasi tutti abbiamo sulle nostre auto una vite di Brugola [io no, ma…], o comunque abbiamo guidato nella vita un’auto che sfrutta questi piccoli oggetti metallici responsabili anche della nostra sicurezza oltre che del funzionamento delle vetture.
Ancora oggi OEB resta una società al cui interno la famiglia Brugola è al comando ed è attivamente coinvolta: dopo Egidio è stato il turno di Giannantonio a cui va dato il merito di aver portato l’azienda nel mondo automotive. Dal 2015 si è passati alla terza generazione, quella di Jody Brugola, all’anagrafe Egidio Stefano, che ha inaugurato l’unico impianto fuori dall’Italia, quello negli Stati Uniti.
Era il 2015, e l’impianto è nato in USA per via delle fortissime sinergie con Ford, senza però mettere in ombra i 5 siti produttivi in Italia tra Lissone e Desio. Da questi siti le viti viaggiano per essere poi smistate in 11 centri logistici nel mondo, ovviamente destinate ad utilizzi più alti e più critici delle viti che chiunque di noi potrebbe acquistare in un negozio di ferramenta, visto che Brugola parla direttamente ai produttori e con gli OEM del mondo auto ha contatti strettissimi che nascono già in fase di progettazione.
Oggi l’azienda impiega 500 dipendenti tra Italia e USA e non ha intenzione né di abbandonare il nostro Paese, né di fermarsi nel processo di innovazione, avendo già abbracciato il mondo dei motori elettrici, espandendosi anche con la produzione di componenti che non sono necessariamente viti, ma restano comunque fondamentali per la mobilità termica o elettrica che sia.
LA PRODUZIONE
Brugola produce oltre 1.000 tipi di viti ad un ritmo di 9 milioni al giorno, tutti pezzi disegnati basandosi sulle specifiche del cliente, ingegnerizzati in casa e pensati per utilizzi ben precisi, ad esempio per le teste dei motori, o per funzioni ancora più critiche come i freni o le ruote.
Si contano sulle dita di una mano le aziende, nel mondo, che hanno la conoscenza e la capacità produttiva che ha Brugola: tramite tecnica dello stampaggio a freddo, dove ogni “colpo” deforma il materiale e crea quindi la vite, si ottiene infatti un prodotto con caratteristiche meccaniche migliori che, inoltre, non crea materiale di scarto.
Il volume che entra nei macchinari è esattamente quello che serve a creare il prodotto finito, poiché anche la filettatura viene fatta per deformazione utilizzando dei “pettini” che evitano la necessità dell’asportazione.
Non fatevi, però, ingannare dal nome: lo stampaggio a freddo non significa che le linee produttive siano attraversate da una piacevole brezza.
Entro infatti in fabbrica e il caldo si fa sentire, con i fuochi dei forni interrotti solo da sistemi di climatizzazione industriale che danno un po’ di refrigerio, ma non permettono di abbattere a sufficienza la temperatura di una giornata in cui anche Madre Natura ci mette del suo con 31°. Ci dicono, però, che in primavera e in autunno si sta molto meglio, e che in inverno il calore generato è convogliato da un sistema di recupero implementato proprio per ridurre gli sprechi ed essere più sostenibili.
Chiacchierando con il personale scopro poi che la tecnica dello stampaggio a freddo “non è una scienza esatta”, ma è frutto di decenni di sviluppo e ogni azienda ha creato nel tempo la sua “ricetta”, un know-how importantissimo e che deve essere protetto e tramandato visto che si tratta di un’eccellenza apprezzata dai tutto il mondo e da marchi come Ford, Renault, Mercedes, BMW, il gruppo Hyundai-Kia e nel 2024 anche il gruppo Stellantis e un altro produttore ancora non ufficialmente comunicabile.
L’acciaio utilizzato arriva dall’Italia, è raccolto in grandi bobine e il filo entra automaticamente nella macchina che si occuperà di tagliarne esattamente la quantità necessaria per produrre il pezzo.
Tramite decappaggio meccanico, alternativa all’utilizzo dell’acido, si evita poi la creazione di “bolle” di idrogeno all’interno della materia prima, rischio porterebbe a spaccare la vite dall’interno con conseguenze in molti casi disastrose.
Le componenti critiche in termini di sicurezza, infatti, hanno parametri molto più stringenti e devono essere trattate solo da operatori esperti.
A prescindere dal fatto che un componente sia critico o meno per la sicurezza degli occupanti della vettura, tutti i prodotti sono comunque analizzati dalle macchine, con fotocamere che effettuano scansioni ad un ritmo forsennato e algoritmi che determinano se il prodotto finito sarà degno del cesto destinato al confezionamento o finirà in quello degli scarti. Scarti che, comunque, non vengono sprecati, ma si controllano ed eventualmente tornano in fonderia per essere riciclati.
Nel corso degli anni, la capacità di rispondere alle specifiche di utilizzi critici e i controlli qualità serrati hanno permesso a OEB (acronimo di Officine Egidio Brugola) di ottenere importanti contratti con il mondo auto, da quello con il gruppo Volkswagen nel 1981 a quello con Ford, prima per il motore I4 nel 1996, poi con l’esclusiva per tutti i motori Ford Europa nel 2006.
QUATTRO CHIACCHIERE CON JODY
Jody è un uomo pragmatico e un imprenditore che non ha paura di sporcarsi le mani. In mezzo alle risposte alle domande di una ristretta tavola rotonda, emerge la figura di un innovatore fedele all’immagine del classico imprenditore brianzolo, di quelli ancora legati a filo diretto con l’azienda e coinvolti attivamente nella sua gestione.
La necessità di tramandare le conoscenze
Interrogato sul futuro dell’azienda, Jody affronta il tema della formazione e della necessità di tramandare le conoscenze ad una nuova generazione che sembra non volersi più confrontare con il lavoro manuale. Nonostante OEB abbia abbracciato tutte le politiche di welfare, con salari già sopra ai minimi e incentivi per le fasce di stipendio più basse, fino a 50.000€, resta l’ombra di un trend forse segnato da un passaggio generazionale.
Per affrontarlo OEB è impegnata su più fronti: la Brugola Academy forma le nuove leve internamente, vista l’alta necessità di specializzazione, e garantisce quasi certamente il collocamento in azienda. Inoltre c’è una costante evoluzione dei macchinari e degli impianti, al fine da semplificare la vita degli operatori in linea, sempre però necessari e fondamentali visto che non è un lavoro che può essere automatizzato con i robot.
Il trend è palese: chi è più giovane, e si sta affacciando al mondo del lavoro ora, non è attratto dai lavori di produzione anche se questi offrono posto fisso, welfare e stabilità, ma questo si ripercuote anche fuori dal contesto aziendale e non esiste più quella generazione fatta di persone che sapevano dove mettere le mani per piccoli lavoretti di manutenzione o riparazione di auto e motorini. La meccanica è diventata poco attraente…
L’elettrico è una minaccia?
Jody non nasconde di preferire, a livello personale, ancora il classico motore endotermico, ma questo non significa essere ciechi di fronte ai cambiamenti, e lo dimostrano le commesse stesse di OEB che stanno crescendo in maniera importante nel mondo elettrico su tutti i fronti. Resta però convinto che il passaggio non sarà immediato, e che il motore termico ha ancora molto da dire: d’altronde le sue viti sono alla base di queste unità, e se restano alti gli ordini e i numeri ci sarà un motivo, no?
Lanciando, come diversi altri imprenditori, un appello alla politica per tracciare una linea chiara visto che ora c’è anche la geopolitica a complicare una transizione energetica che sembrava scritta sulla pietra, Jody risponde che OEB comunque è destinata a crescere, a prescindere dalla direzione che prenderà il vento. Brugola è pronta alla conversione, qualora questa dovesse essere definitiva, e ha già chiari i piani di espansione.
E la sostenibilità?
Si tratta di un tema caro a Jody, sostenitore di molte iniziative in OEB. Nel 2019 è iniziato il processo di eliminazione della plastica all’interno del processo di produzione, compensando il 20% che non poteva essere eliminato. Anche la carta usa e getta è stata eliminata, rimpiazzata con panni tecnici lavabili e riutilizzabili, e sono state abbracciate iniziative di compensazione di CO2 oltre all’utilizzo dei LED, il convogliamento del calore dei reparti produttivi al resto dell’edificio per il riscaldamento, la scelta di nuovi inverter per i macchinari (più efficienti) o il progetto di coltivazione aeroponica utilizzando la CO2 emessa per le piante che saranno poi usate dalla mensa a chilometro zero che aprirà il prossimo anno in un vecchio edificio in disuso da attrezzare con fotovoltaico e con le ultime tecnologie di risparmio energetico.
Il processo forse più importante è ancora in corso d’opera: si tratta del recupero degli oli che sono onnipresenti e fondamentali nella produzione. Il primo anno, però, ha dato risultati molto incoraggianti perché sono 100 le tonnellate recuperate al fine di impiegarle nuovamente. Il lavoro ovviamente prosegue e da un lato si punta ad aumentare la quota recuperata, dall’altro si vuole ridurre il consumo, sia di olio, sia di gas per le sei linee forno.
Alla fine del processo, tutto il residuo di emissioni che non sarà stato possibile eliminare, sarà compensato con il progetto di Forever Bambù già avviato nel 2021 per la creazione di nuove foreste in Italia.
Le viti sono in pericolo?
Telai con stampaggio per pressofusione, ricerca spasmodica della riduzione dei pesi e stampa 3D sono minacce per le viti? Credo di no, c’è stato il trend della colla in passato, ma le viti sono sopravvissute. Hanno una tecnologia che può sembrare stupida ma è molto funzionale e le stampanti 3D sono sì un ottimo strumento per la prototipazione, ma non sono in grado di reggere i ritmi e le quantità necessarie nel mondo della produzione. Il progresso può dare una mano allo sviluppo, ma deve essere sfruttato bene e con senno.